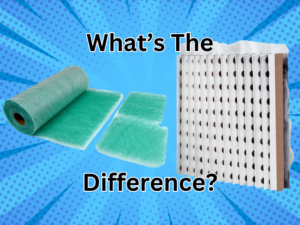
A Guide to Spray Booth Filters
Understanding spray booth filters is crucial for anyone working in industries that involve painting, coating, or any form of finishing application. Spray booth filters play a vital role in maintaining a safe and clean working environment while ensuring the quality and efficiency of the painting process.
Understanding spray booth filters is essential to ensure worker safety. When spraying paint particles, they become airborne and can pose health hazards if not properly filtered.
These particles can contain harmful chemicals, volatile organic compounds (VOCs), or other toxic substances that can be detrimental to human health if inhaled or absorbed through the skin. By comprehending how spray booth filters function and their different types, workers can take necessary precautions to minimize exposure risks.
Moreover, understanding spray booth filters is vital for complying with environmental regulations. Painting operations often release volatile organic compounds into the atmosphere, contributing to air pollution and potential harm to the ecosystem. For more details, visit documentation from the EPA for more information.
Spray booth filters effectively capture these particles before releasing them into the environment, ensuring compliance with local and national emissions control regulations. Understanding spray booth filters also helps maintain high-quality finishes, which is important for worker safety and environmental compliance.
Particulate matter such as dust or lint can easily contaminate freshly sprayed surfaces if not filtered out appropriately by the system’s filters. This contamination leads to defects like rough texture or imperfections on painted surfaces.
Thus, comprehending how paint booth filters function enables users to select the right type of filter for specific applications, ensuring that only clean air circulates within the spraying area. Ultimately, grasping the importance of understanding spray booth filters empowers individuals involved in painting processes to make informed decisions when it comes to filter selection and maintenance.
It promotes a safer work environment while adhering to environmental standards and ensures top-notch finishing results that meet industry expectations. By diving deeper into this topic’s intricacies – such as filter types and contaminants filtered – one can fully appreciate their significance in maintaining efficient operation and achieving desired outcomes.
The Function of Spray Booth Filters
Spray booth filters play a crucial role in ensuring the efficiency and safety of spray booths. These filters are effectively capture and remove contaminants from the air. providing a clean working environment for operators and preventing pollutants from being in the atmosphere. Understanding the function of spray booth filters is essential for anyone involved in spray painting or operating a spray booth facility.
One primary function of spray booth filters is to remove solid particles from the air. When paint or coating materials, tiny particles become airborne, creating overspray.
Airborne overspray particles can settle on surfaces, leading to defects in the finish or contaminating other workpieces. Spray booth filters act as barriers that capture these particles before they have a chance to settle, preventing contamination and maintaining a high-quality finish.
Spray booth filters capture solid particles and eliminate VOCs from the air inside the booth.VOCs are gases from paint and coatings that can be harmful when inhaled or released into the environment.
By using specialized filter media, such as activated carbon or catalytic materials, VOCs can be adsorbed or chemically transformed into less harmful substances before being discharged. Another important function of spray booth filters is to control airflow within the booth itself.
Proper airflow is essential for achieving uniform coating thicknesses and minimizing drying times. Filters provide resistance against airflow, allowing technicians to adjust ventilation rates according to specific requirements.
This control helps optimize paint drying processes by ensuring an adequate exchange of clean air while avoiding excessive turbulence that could disturb freshly applied coatings. Spray booths also need proper ventilation for operator safety reasons during painting operations.
Filters contribute significantly by removing hazardous chemical fumes and odors generated during spraying processes before they reach operators’ breathing zones. The installation of appropriate exhaust filters effectively mitigates health risks associated with exposure to harmful substances commonly found in paints and coatings.
Understanding the function of spray booth filters is crucial for maintaining the quality of paint jobs, protecting the environment, ensuring operator safety, and optimizing spray booth performance. By effectively capturing solid particles, removing VOCs, regulating airflow, and filtering out hazardous fumes, these filters play a vital role in creating a clean and controlled environment within spray booths.
Types of Contaminants Filtered
When it comes to understanding spray booth filters, it is crucial to familiarize oneself with the various types of contaminants that these filters are designed to capture. In a spray booth environment, different contaminants can be present, depending on the nature of the work being performed. Here are some common types of contaminants that spray booth filters are capable of filtering out:
1. Overspray: One of the primary contaminants found in a spray booth is overspray, which refers to the excess paint particles that do not adhere to the intended surface during painting or coating processes. These fine particles can easily become airborne and create a hazardous working environment if not properly filtered.
2. Dust and Dirt: Dust and dirt particles are ubiquitous in any workspace, including spray booths. These microscopic particles can settle onto freshly painted surfaces and cause imperfections or defects in the final finish if not removed by effective filtration.
3. Vapors and Fumes: Spray booths often contain harmful vapors and fumes generated from solvents, paints, coatings, adhesives, or other chemicals used in the process. These volatile organic compounds (VOCs) pose health risks to workers if inhaled directly from the air within the booth.
4. Debris: In some cases, larger debris such as lint fibers or manufacturing byproducts might find their way into a spray booth through ventilation systems or other means. These objects can contaminate freshly painted surfaces or clog up filters if not effectively filtered out.
5. Biological Contaminants: Depending on specific work conditions or environmental factors, biological contaminants such as mold spores or bacteria may be present within a spray booth environment. Effective filtration systems should be capable of capturing these microorganisms to maintain a clean working atmosphere.
Manufacturers and operators must understand that filters to capture specific contaminants more efficiently. Knowing the types of contaminants in a spray booth helps in selecting the right filters for optimal air quality and safety.
Intake Filters
When it comes to spray booth filters, one of the key components is the intake filter. They play a crucial role in ensuring that the air entering the spray booth is clean and free from contaminants.
These filters are designed to capture large particles and prevent them from entering the booth, thus maintaining a clean working environment. There are different types of intake filters available for spray booths, each with its own unique features design, and advantages.
Polyester intake filters and are the most common and have smaller pore sizes which allow them to capture even finer particles like pollen and mold spores. These come in many styles but the most popular styles are Intake blankets and Intake panels also known as R1 Pad.
R1 panels / panels have a wire frame to keep them in place and are used more frequently in crossdraft style booths.
Intake blankets are the most common types of filters used in paint booths and are located in the ceiling. Paint booth blankets are used for many manufacturers including Blowtherm, GFS, and Garmat.
For example, garmat ceiling filters are most common in sizes of 38″x62″ and 38″x107″
They are also highly resistant to moisture, making them ideal for environments with high humidity levels.
To ensure optimal performance of intake filters, regular maintenance is essential. This includes monitoring their condition regularly and replacing them when they become clogged or damaged.
The frequency of replacement may vary depending on factors such as usage intensity, type of contaminants being, and environmental conditions. Intake filters form an integral part of any spray booth system by preventing large particles from entering the working area during painting operations. Paint booth ceiling filters are use 1 time a year normally and R1 pads are changed 2 times a year normally.
Regular maintenance and replacement of intake filters are crucial to maintaining a clean and efficient working environment, ultimately ensuring high-quality finishes in spray painting applications.
Fiberglass Spray Booth Filters
Fiberglass filters are one of the most commonly used filters in spray booths due to their excellent filtration capabilities. These filters are made from layers of fine fiberglass fibers that capture and retain particles as they pass through the filter media.
The fibers are dense mat, creating a high-efficiency filter that effectively traps overspray, dust, dirt, and other contaminants. One notable feature of fiberglass spray booth filters is their high holding capacity.
The dense arrangement of fiberglass fibers allows these filters to hold a significant amount of overspray before requiring replacement. This makes them an ideal choice for applications involving high volumes of spraying or environments with heavy levels of contamination.
In terms of filtration efficiency, fiberglass spray booth filters excel at capturing paint overspray. The fine fibers create a maze-like structure that forces air to change direction multiple times, increasing the chances for particle capture.
Fiberglass exhaust filters are available in fiberglass pads or in fiberglass rolls. Many sizes of filters are available depending on your type of booth and location of where the exhaust exits the booth.
20″x20″ exhaust fiberglass pads are most commonly used in a paint booth where the exhaust is on a wall, where a fiberglass filter roll would be used on a floor for a downdraft paint booth.
Fiberglass spray booth filters offer excellent filtration, good holding capacity, and cost-effectiveness. Their versatility makes them ideal for industries requiring airborne particle control and superior paint finishes.
Polyester Spray Booth Filters
Polyester filters are a popular choice for their excellent filtration capabilities and longevity.
These filters are tightly woven polyester layers, creating a dense barrier against particulates. Their high dust-holding capacity allows them to capture and retain significant overspray effectively.
One notable characteristic of polyester spray booth filters is their ability to capture smaller particles compared to other filter types. This is due to the fine weave structure of the polyester media, which traps tiny particles that might otherwise escape through other filter materials.
These filters offer superior protection for workers and the environment by minimizing airborne contaminants. Additionally, polyester spray booth filters offer excellent airflow characteristics.
Their design allows air to flow with minimal resistance, balancing filtration efficiency and pressure drop. This ensures consistent airflow, even as the filter collects overspray, maintaining an efficient work environment for painters.
Another advantage of using polyester filters is their durability. They have exceptional resistance against tearing or deformation under high-velocity airflows typically found in spray booths.
This sturdiness ensures that the integrity of the filter remains intact during operation, preventing any bypassing or leakage that could potentially compromise overall filtration efficiency.
Polyester spray booth filters efficiently capture overspray particles of varying sizes while maintaining airflow and durability. Making them an excellent choice for reliable, long-lasting filtration.
Exhaust Filters
In the realm of spray booth filters, exhaust filters play a vital role in maintaining a clean and contaminant-free environment.
These filters capture overspray and fine particles live during spraying, preventing their release into the surrounding atmosphere. One popular type of exhaust filter is the pleated paper filter.
Some specialty booths use Carbon filters are designed with activated carbon media that effectively absorb and neutralize odors and harmful gases emitted during painting processes. This is particularly important when working with paints that contain volatile organic compounds (VOCs) or other hazardous substances.
The activated carbon acts as a powerful adsorbent, trapping these pollutants and preventing their release into the surrounding environment. Different spray booth setups may need specific exhaust filter configurations based on size and ventilation needs.
Some booths may incorporate multiple stages of filtration in order to achieve optimal air quality standards. This may involve using pre-filters for larger particles and post-filters to enhance air purification.
Regular maintenance and inspection play a crucial role in ensuring optimal performance of exhaust filters. Periodically checking these filters for clogging or damage is essential as it can directly impact their effectiveness.
If saturation airflow occurs, promptly replace the exhausted filters to maintain air quality within the spray booth. Exhaust filters are crucial in spray booth systems, capturing overspray particles and removing harmful contaminants during painting.
Pleated paper and advanced carbon filters ensure efficient filtration for cleaner air in the spray booth. Regular maintenance and timely filter replacement are essential for optimal performance and a safe work environment.
Advanced Carbon Filters
The carbon material typically comes from sources like coconut shells or coal and undergoes activation to enhance its adsorption properties. One of the key advantages of advanced carbon filters is their ability to capture and retain a wide range of VOCs.
These filters use adsorption, where VOC molecules in the air are attracted to the porous carbon structure. As the air passes through the filter, these molecules become trapped within its internal surface area.
The effectiveness of advanced carbon filters largely depends on their contact time with the contaminated air stream. For this reason, some manufacturers incorporate multiple layers or beds of activated carbon into their filters.
This increases surface area for adsorption, ensuring longer contact time. Advanced carbon filters may also use additives to enhance performance against specific contaminants.
The rate of filtration depends on factors like pollutant concentration, airflow, temperature, humidity, and filter size. Therefore, regular monitoring and maintenance are essential to ensure optimal filtration efficiency.
Advanced carbon filters provide excellent odor control and effectively remove VOCs from spray booth exhaust air. Proper care and timely replacement, following guidelines, keep spray booths clean and reduce airborne health risks.
Maintenance and Replacement Schedule for Filters
Proper maintenance and timely replacement of spray booth filters are crucial to ensure optimal performance and safety. Neglecting this aspect can result in poor air quality, reduced efficiency, and potential health hazards.
To maintain the longevity of the spray booth system, it is essential to establish a regular maintenance schedule. Regular inspection is the first step in maintaining spray booth filters.
This is done monthly to check for any signs of damage or clogging. Inspect both intake and exhaust filters meticulously, paying attention to dust accumulation, discoloration, tears, or any other visible defects.
Additionally, monitor filter pressure drop levels using a differential pressure gauge as an indicator of when they need replacement. Filter replacement frequency depends on factors like contaminant type and the volume of work in the booth.
These generally last between 4 to 6 months before requiring replacement; however, this may vary depending on usage. Ceiling filters may last up to a year depending on conditions.
These high-performance filters can last up to a year before needing replacement but should still periodically for saturation levels. It is important to keep accurate records of filter replacements, inspections, and maintenance. Proper maintenance and regular replacement of spray booth filters are essential for maintaining optimal air quality, efficiency, and safety.
Conclusion
Understanding spray booth filters is crucial for maintaining a safe and efficient spray booth environment. The proper function of these filters ensures that harmful contaminants are efficiently, providing a clean and pollution-free workspace.
By understanding the contaminants they filter, such as dust, paint overspray, and VOCs, operators choose optimal filters.. Intake filters are capture particles and prevent them from entering the spray booth area, allowing for quality paint finishes.
Exhaust filters play a vital role in eliminating hazardous substances before releasing air into the atmosphere. Fiberglass paint booth filters are common for exhaust filtration as well polyester filters.
Additionally, advanced carbon exhaust filters provide an extra layer of purification by absorbing odors and VOCs. Regular maintenance and replacement of spray booth filters should be a priority to ensure consistent performance.
Following a predetermined schedule will prevent filter saturation or clogging, guaranteeing optimal filtration efficiency throughout operations. Understanding spray booth filters helps operators recognize their role in maintaining a safe, contaminant-free environment.
Choosing the right intake and exhaust filters boosts productivity and ensures environmental compliance for businesses. Regular maintenance helps spray booths perform optimally, protecting workers’ health and maintaining air quality.