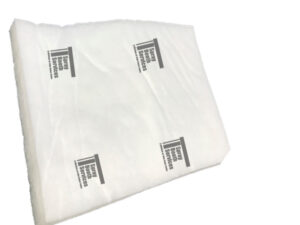
Introduction to Spray Booth Ceiling Intake Filters
Spray booth ceiling intake filters play a crucial role in maintaining clean and safe working environments within industrial spray booths. These filters are specifically designed to capture and remove various contaminants from the air, ensuring that the air inside the booth remains clean and free from harmful particles. By effectively filtering out dust, overspray, paint mist, chemical fumes, and odors, these filters contribute significantly to the overall efficiency and quality of spray booth operations.
Definition and Purpose of Spray Booth Ceiling Intake Filters
Spray booth ceiling intake filters are specialized devices installed in the upper section of spray booths. Their primary purpose is to capture airborne contaminants that enter through the booth’s ceiling during painting or other related processes.
These filters act as the first line of defense against harmful particles by trapping them before they have a chance to circulate throughout the working area. By removing these contaminants effectively, spray booth ceiling intake filters enhance worker safety while also preventing damage to equipment or finished products.
Importance of Proper Filtration in Spray Booths
Proper filtration is paramount within spray booths due to several reasons. Firstly, it ensures compliance with health and safety regulations by minimizing workers’ exposure to hazardous substances present in paint fumes or chemicals used during coating processes. Without effective filtration systems in place, workers may suffer from respiratory issues or other health concerns associated with prolonged exposure to these air pollutants.
Secondly, maintaining a clean environment inside spray booths is essential for achieving high-quality results in industrial painting applications. Contaminants such as dust particles or overspray can settle on freshly painted surfaces if not adequately filtered out.
This leads to imperfections on finished products, compromising their appearance and durability. Proper filtration contributes significantly to prolonging the lifespan of equipment and improving operational efficiency.
By preventing contaminants from reaching critical machinery or clogging ventilation systems, filters help reduce maintenance costs and downtime associated with equipment breakdowns. Additionally, clean air circulation promotes consistent airflow patterns within the booth, ensuring optimal paint application and reducing the risk of defects caused by uneven drying or curing.
Understanding the Functionality of Spray Booth Ceiling Intake Filters
Explaining the Intricacies of Spray Booth Ceiling Intake Filters
Spray booth ceiling intake filters are an integral part of maintaining a clean and safe working environment in spray booths. These filters work by employing a combination of physical and chemical filtration mechanisms to capture and trap various contaminants present in the air. As air is drawn into the spray booth through the ceiling intake, it passes through the filter media, which is designed to effectively capture particles suspended in the air.
The filter media structure allows for proper airflow while ensuring maximum filtration efficiency. This ensures that only clean air is circulated within the booth, protecting both workers and finished products from harmful particles.
Types of Contaminants Filtered by Spray Booth Ceiling Intake Filters
Spray booth ceiling intake filters play a vital role in removing a wide range of contaminants commonly found in spray booths. These filters effectively capture dust particles and debris, preventing them from settling on freshly painted surfaces or mixing with paint during application.
Additionally, they excel at capturing overspray and paint mist generated during painting operations, preventing these particulates from escaping into surrounding areas or being recirculated within the booth. Furthermore, high-quality spray booth ceiling intake filters provide effective removal of chemical fumes and odors that can be hazardous to workers’ health or compromise product quality.
Dust Particles and Debris: Shielding Your Work From Imperfections
Dust particles and debris are ubiquitous environmental contaminants that pose significant challenges when it comes to achieving a flawless finish on painted surfaces. The intricate design of spray booth ceiling intake filters ensures efficient removal of these unwanted particles before they settle on freshly painted surfaces. By capturing these minuscule impurities suspended in the air, these filters help mitigate imperfections caused by dust specks or debris landing on wet paint, resulting in a smoother and more professional finish.
Overspray and Paint Mist: Preserving the Integrity of Your Workspace
Overspray and paint mist are inevitable byproducts of the painting process. These fine particles become airborne during spraying, creating a potential hazard if left unfiltered.
Spray booth ceiling intake filters efficiently capture overspray and paint mist, preventing them from settling on the floor or escaping into the surrounding environment. By containing these particles within the booth, these filters not only maintain a clean workspace but also reduce the risk of contamination in adjacent areas or damage to other equipment in the facility.
Chemical Fumes and Odors: Safeguarding Workers’ Health
The chemicals used in paints often release fumes that can be harmful to workers if inhaled over an extended period. Spray booth ceiling intake filters provide effective chemical filtration by capturing volatile organic compounds (VOCs) and other odorous substances present in spray booth air. This ensures that workers are protected from potentially hazardous chemical fumes, promoting a healthier working environment while reducing health risks associated with long-term exposure.
By understanding how spray booth ceiling intake filters function and their ability to filter out different types of contaminants such as dust particles, overspray, paint mist, chemical fumes, and odors, one can appreciate their role in maintaining high air quality within spray booths. This knowledge underscores the importance of selecting appropriate filters based on specific needs while ensuring worker safety and product integrity.
Different Types of Spray Booth Ceiling Intake Filters
Fiberglass Filters
Fiberglass filters are among the most commonly used filters in spray booth ceiling intake systems. These filters consist of layered fiberglass fibers that create a dense web-like structure capable of capturing a wide range of contaminants. Fiberglass filter technology relies on the principle of mechanical filtration, where particles are trapped within the filter’s fibers as air passes through.
One advantage of using fiberglass filters is their affordability and availability in various sizes and thicknesses, accommodating different spray booth configurations. However, it’s important to note that fiberglass filters tend to have lower filtration efficiency compared to other options and may need more frequent replacement due to their lower dust holding capacity.
Pleated Panel Filters
Pleated panel filters offer an alternative to fiberglass filters with enhanced performance and durability. These filters consist of pleated media made from materials like polyester or synthetic fibers, providing a larger surface area for improved particle capture.
The pleated design allows for better airflow while maintaining filtration efficiency. Pleated panel filters are particularly effective in trapping fine particulate matter, including overspray and paint mist.
They also have a higher dust holding capacity compared to fiberglass filters, resulting in extended service life before requiring replacement. However, it’s worth noting that pleated panel filters can be more expensive than fiberglass options.
High-Efficiency Particulate Air (HEPA) Filters
HEPA filters represent the pinnacle of air filtration technology when it comes to spray booth ceiling intake systems. These advanced filters adhere to strict industry standards by capturing 99.97% of particles as small as 0.3 microns in size, ensuring exceptional air quality within spray booths.
HEPA filters are commonly used in spray booths where strict regulations demand the highest level of air purification, such as in medical device manufacturing or aerospace industries. However, due to their superior performance, HEPA filters tend to be more expensive upfront and may require specialized equipment for installation.
IV: Factors to Consider When Choosing Spray Booth Ceiling Intake Filters
A: Filtration Efficiency
Filtration efficiency is a crucial factor when selecting spray booth ceiling intake filters. The Minimum Efficiency Reporting Value (MERV) rating system commonly measures the effectiveness of air filters, including those in spray booths.
Understanding MERV ratings helps determine a filter’s ability to capture particles of varying sizes. Higher MERV ratings indicate greater filtration efficiency; however, it’s important to strike a balance between filtration power and maintaining adequate airflow for proper ventilation.
B: Filter Longevity and Maintenance Requirements
Considering the lifespan of different filter types is essential to ensure optimal performance and minimize frequent replacements. While fiberglass filters may have lower initial costs, they generally have a shorter service life due to their limited dust holding capacity.
Pleated panel filters offer a longer lifespan with increased dust holding capacity but might require periodic maintenance such as cleaning or replacing damaged pleats. HEPA filters for long-lasting performance to other options, but it’s important to handle them with care during maintenance or replacement to ensure they continue to work effectively.
C: Cost Considerations
Cost considerations play an important role in choosing the right spray booth ceiling intake filter without compromising quality. While initial costs vary among different filter types, it’s crucial to take into account long-term savings achieved through reduced replacements or improved energy efficiency attributed to better performing filters. Balancing both affordability and effectiveness ensures long-term cost-effectiveness while maintaining high air quality standards within spray booths.
V: Installation and Replacement Procedures
Proper installation and regular filter replacement are vital for maintaining optimal performance in spray booth ceiling intake systems. Consult the manufacturer’s guidelines for specific installation instructions, ensuring filters are securely and correctly positioned to prevent air leaks and maintain proper airflow.
Regular filter maintenance, such as cleaning or replacing based on the manufacturer’s recommendations, is essential to avoid clogging, which can lead to decreased filtration efficiency or strain on ventilation systems. Following proper procedures helps prolong filter lifespan, maintain air purity, and ensure a healthy working environment.
Conclusion
Choosing the right spray booth ceiling intake filters is crucial for achieving high-quality air filtration in spray booths. Understanding the different types of filters available, such as fiberglass filters with their affordability but lower efficiency, pleated panel filters combining performance with longevity or HEPA filters providing superior filtration power, allows for informed decision-making.
Considering factors like filtration efficiency, filter longevity and maintenance requirements, as well as cost considerations ensures a well-rounded approach to selecting the most suitable filter for specific needs. By following proper installation procedures and adhering to recommended maintenance protocols, spray booth operators can create an environment that promotes safety and maintains optimum air quality throughout their operations.